Energy Balancing System
Energy-saving technical services include:
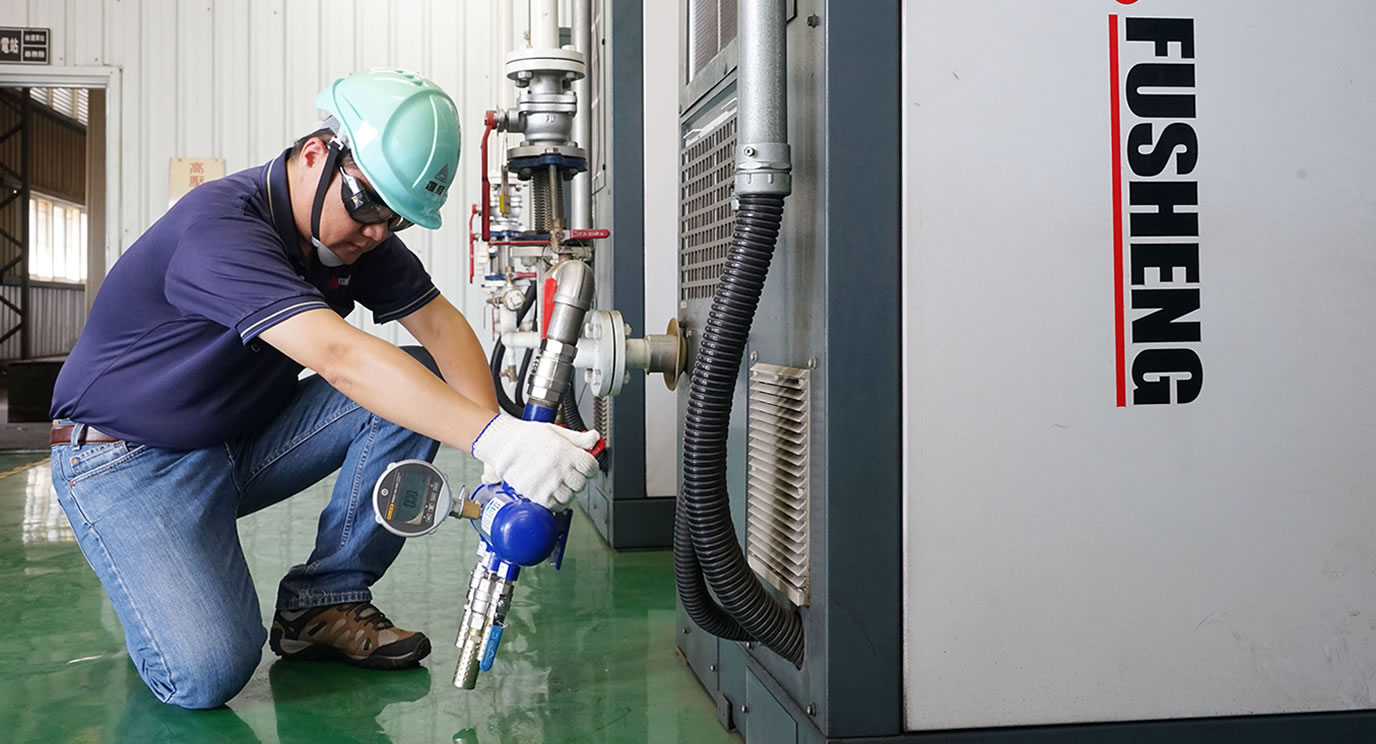
Purpose:
To understand the current performance of the equipment, and to use as the basis for future replacements
Practice:
An orifice flowmeter, digital pressure gauge, and thermometer are used to measure the airflow output and power consumption of the air compressor at full load to understand the efficiency of the equipment under rated conditions. Measurements of current usage efficiency can also be assessed for users.

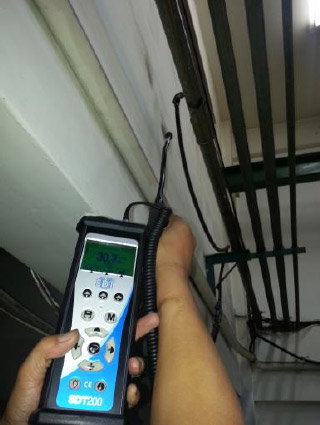
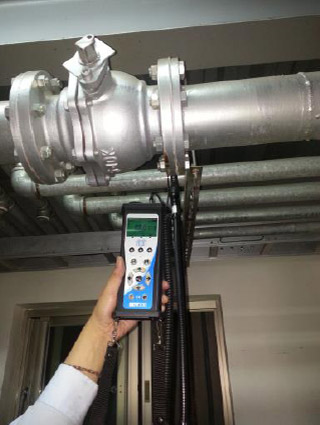
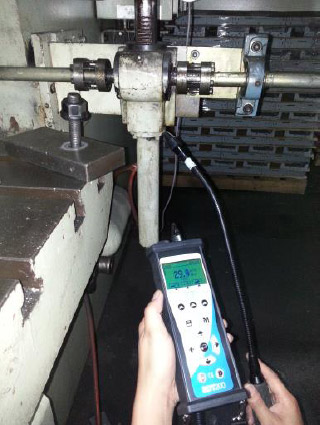
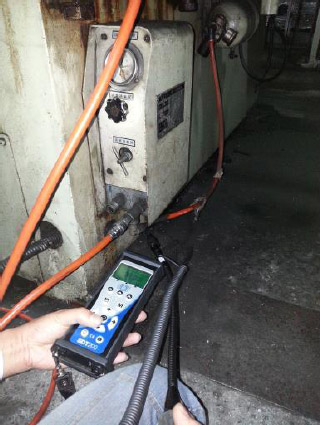
Purpose:
A typical factory compressed air leakage accounts would for about 10~30% of the total gas consumption. Effectively finding and fixing the source(s) of leakage can reduce false demands for compressed air. In others words, energy saving can be achieved immediately without big budgets.
Practice:
An ultrasonic leak detector is used to find the source(s) of the leak and calculate the amount of compressed air wasted according to sound frequency detected from the pressure inside the tube and at the point of leakage. The annual cost wasted due to the leakage can also be derived.
Purpose:
To find the optimal air volume control operation mode of air compressor systems based on the variation of air volume at maximum, minimum and average gas consumption. By reducing the compressor unloading time, the amount of energy wasted is also reduced.
Practice:
The setting of pressure differences between air compressors is used in determining the ordering of main and assisting compressors. Loading regulations could also be conducted through a remote intelligent sequence controller.
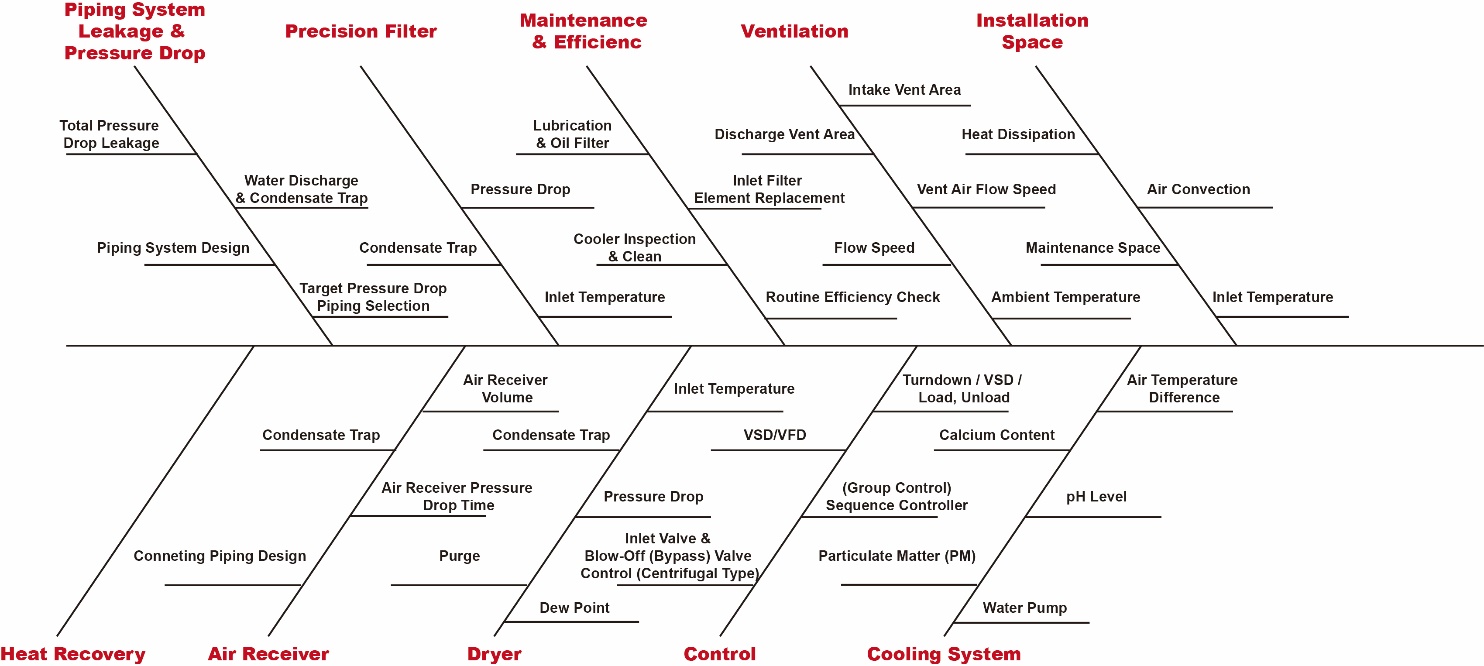
Purpose:
To optimize energy savings in an existing compressed air system.
Practice:
Conduct a ten-step energy audit on the compressed air system and search for energy usage improvement opportunities to undergo brief evaluations. Any detailed assessment would require further measurement and diagnosis, which includes single unit efficiency measurements, system gas consumption analysis, leak point lookup...etc.
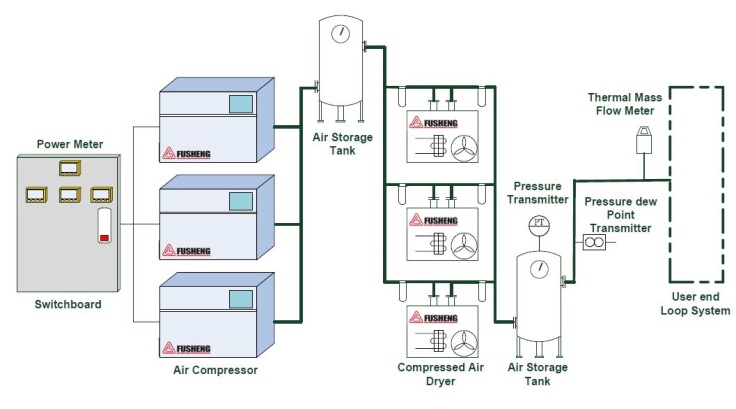
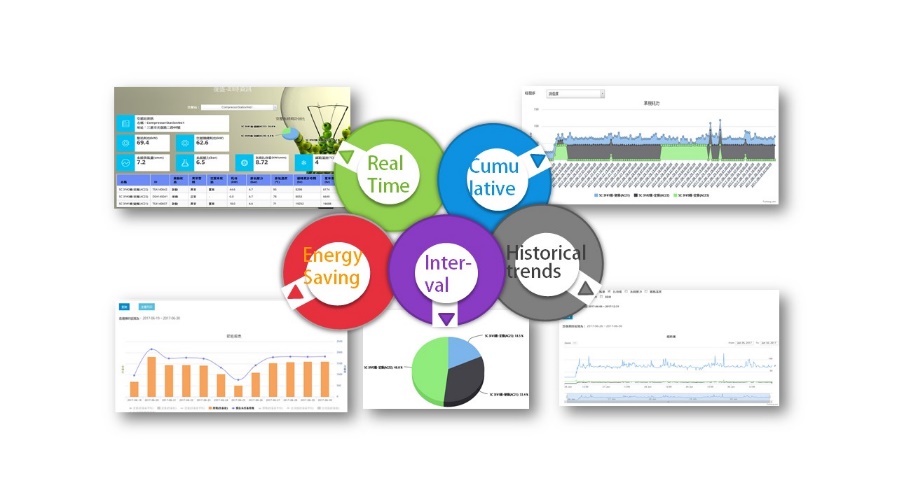
Purpose:
The goal behind the ISO50001 energy management system is to ensure the continuous improvement of energy efficiency. The energy monitoring management platform allows users to keep track of the current energy usage status of existing compressed air systems and to detect every potential way to improve energy efficiency of the compressed air system.
Practice:
Air compressed systems can be built with sensors related to energy measurements, such as electricity meters, pressure sensors, pressure dew point sensors, flow meters...etc. The data measured by each sensor are transferred to Fusheng’s GoService cloud system’s EnMS platform through the advanced IoT technology, which allows users to view the real-time energy usage status of the compressed air system through the online network.
Benefits:
- Customized designs: The design of air compressor system fields may vary from one another; therefore, in order to satisfy the needs of users, we provide customized designs for the user.
- Compressors are integrated with IoT-based information systems to reduce the user’s time needed for manual recording. In addition, the system’s real-time energy use status can be easily accessed through the online network.
- The system actively analyzes the effectiveness of air compressors before and after energy saving improvement(s). A baseline is established before changes are made, and performance is compared after improvements. With this system, it reduces the need for multiple manual measurements.
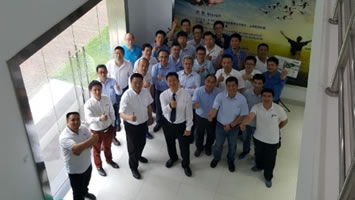
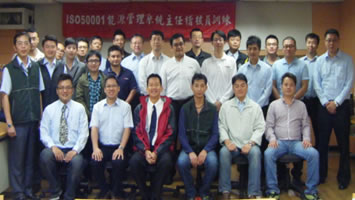
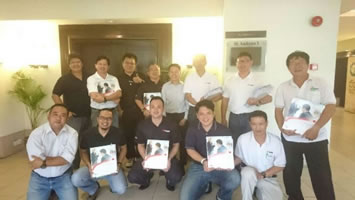
Fusheng has over 180 professional staff members in Taiwan, China, and the Asia Pacific. Each member has obtained the ISO50001 EnMS Lead Auditor certificate. In addition, there are five that have obtained the CMVP International Certificate.

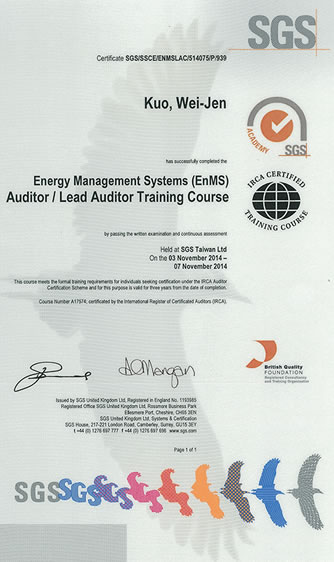